Popular Marine A/C Water Cooled Chillers
60,000 BTU(5 TON) Water Cooled Marine A/C Chiller
Flagship Marine’s extremely compact 5-ton (60,000 BTU) reverse-cycle heat pump marine A/C chiller is only 16” x 23” x 28” (407mm x 584mm x 711mm)
180,000 BTU (15 TON) Water Cooled Marine A/C Chiller
Our typical extreme duty 15 ton marine chiller specifically designed for the US Navy
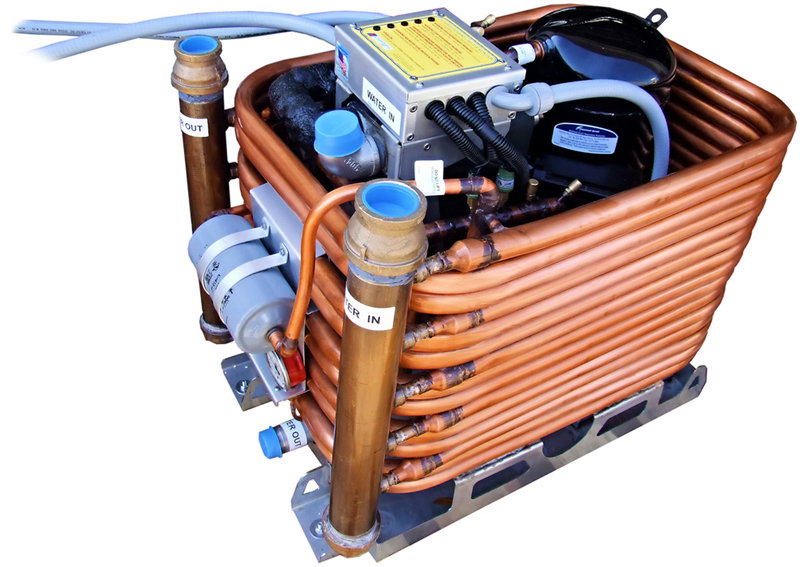
This 15 ton (180,000 BTU) marine air conditioning chiller with a bulletproof Copeland ZP154 scroll compressor (155,000BTU air cooled – we DON’T skimp!)
120,000 BTU(10 TON) Water Cooled Marine A/C Chiller
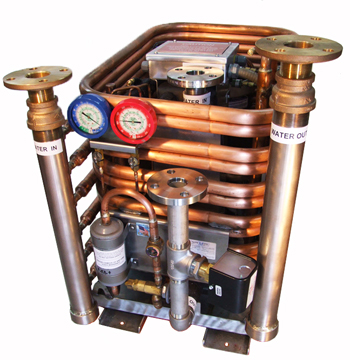
This 10 ton extreme-duty marine chiller has been designed for sea water temperatures of up to 105°F and is fitted with optional sea water manifolds with 150# four bolt flanges.
360,000 BTU (30 TON) Water Cooled Marine A/C Chiller
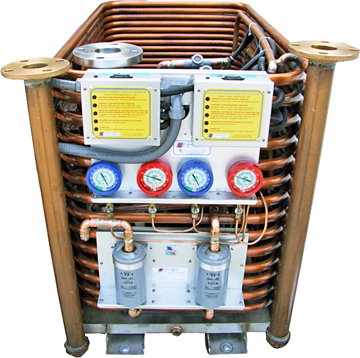
This 360,000 BTU dual compressor marine air conditioning chiller has an incredible 31″ x 52″ footprint and is only 39″ tall.
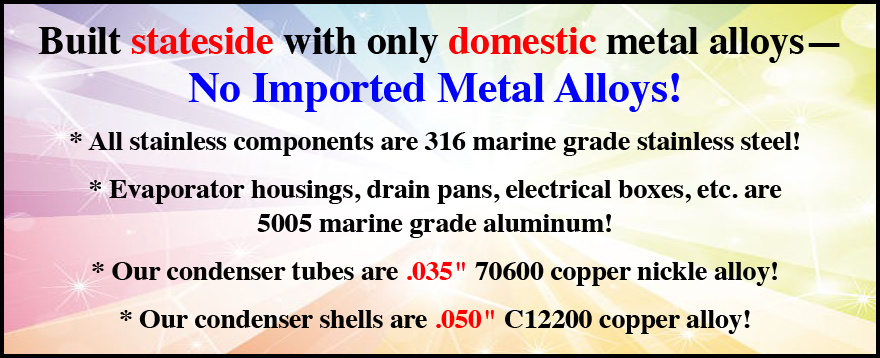
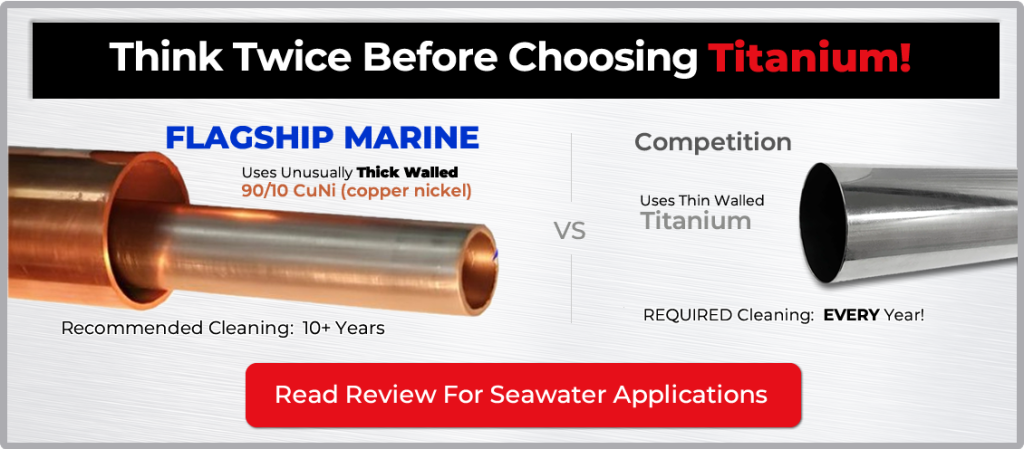
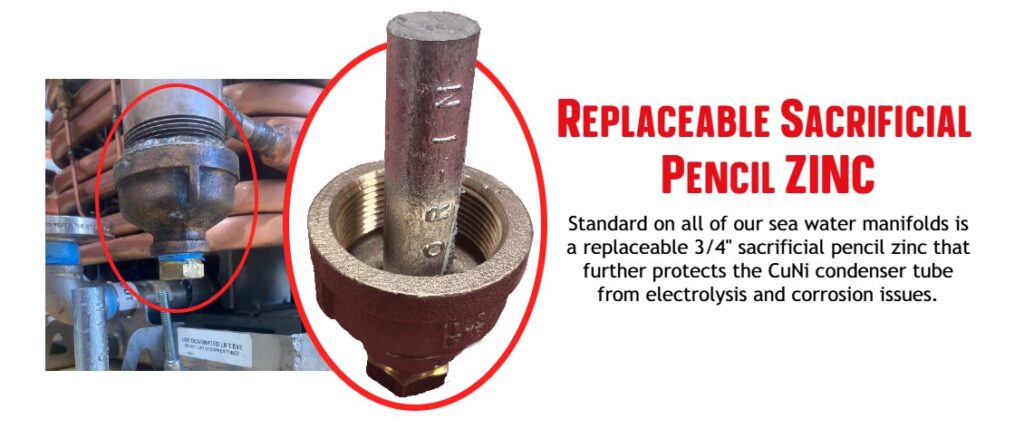
Marine A/C Water Cooled Chillers Specifications
Month | BTUs of Cooling | Specs | Length/Width/Height in inches/mm |
Amps (cool) 230v | Weight lbs/kg | Buy Now |
---|---|---|---|---|---|---|
FM24CW View Image | 24,000 | Manual & Drawing | 25"/15.5"/23" 635/394/585 |
11.4 | 110/50 | Buy Now |
FM36CW View Image | 36,000 | Manual & Drawing | 25/15.5"/23" 635/394/585 |
16.4 | 121/55 | Buy Now |
FM48CW View Image | 48,000 | Manual & Drawing | 25"/15.5"/23" 635/394/585 |
22 | 179/81 | Buy Now |
FM60CW View Image | 60,000 | Manual & Drawing | 25"/15.5"/23" 635/394/585 | 28 | 210/95 | Buy Now |
FM96CW View Image | 96,000 | Manual & Drawing | 32"/19.5"/24" 813/496/585 |
24.3@230/3 | 340/154 | INQUIRE |
FM120CW View Image | 120,000 | Manual & Drawing | 32"/19.5"/24" 813/496/610 | 33.3@230/3 | 490/222 | INQUIRE |
FM180CW View Image | 180,000 | Manual & Drawing | 32/19.5/29 813/496/737 | 19.6@460.3 | 625/283 | INQUIRE |
FM240CW View Image | 240,000 | Manual & Drawing | 47.5/26/24.5 1207/661/623 | 35.0@460/3 | 980/444 | INQUIRE |
FM360CW View Image | 360,000 | Manual & Drawing | 47.5"/26"/31.75" 1207/661/807 | 39.2@460/3 | 1,147/520 | INQUIRE |
Marine A/C Chiller Configuration & Installation
Our FM360CW Water Cooled Marine A/C Chillers
preparing to be shipped off from our manufacturing facility in Stuart FL.
Marine A/C Water Cooled Chiller Featues
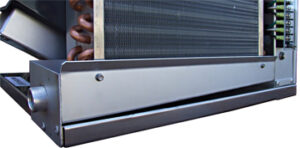
Flagship Marine Exclusive: Dry Drain Pan
No more mold and mildew starting in your drain pan! Flagship Marine takes pride in its exclusive innovation for marine air conditioning systems — the Dry Drain Pan. This cutting-edge feature revolutionizes the conventional drain pans utilized in all Flagship Marine’s chiller AC systems. Crafted from durable sloped aluminum, these drain pans ensure a moisture-free environment, preventing the accumulation of condensate water that often leads to the growth of mold and mildew.
All sheet metal components are laser cut
All sheet metal components are laser cut with aircraft/military quality tolerances in the ten-thousandths of an inch range as depicted here with the skeleton of an air-cooled marine air conditioning chiller. Note the PEM nut inserts and numerous stainless steel rivets that result in a very rigid, strong and exacting structure.
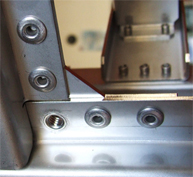
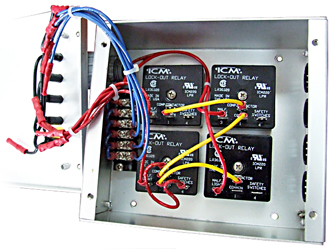
Flagship's Exclusive Diagnostic Monitors
With Flagship there are no expensive proprietary printed circuit boards. No highly trained technician needed, typically a voltmeter and a screwdriver is all that is needed to make most repairs!
All Flagship Water Cooled Marine A/C Chillers have a low voltage control module with clearly labeled LEDs advising the end user specifically what has tripped the marine chiller, be it high or low refrigerant pressure, freeze control protection as well as low chilled water flow.
Chiller Electric Box
What sets Flagship Marine apart from our competition is our belief in the KISS principle (Keep It Simple, Stupid). This has guided our component selection and design emphasis for many years. We brag that even a child can follow our schematics!
Look at this single compressor chiller electric box. All the components are “over the counter” at a fraction of typical costs in our industry. The most expensive item here is less than $53.00!
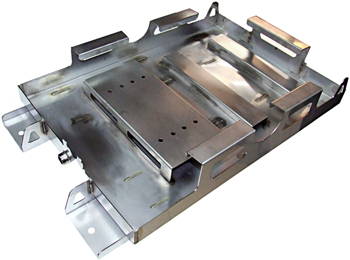
Our 14 gauge, 316 Series
Our 14 gauge, 316 Series stainless steel, one-piece, precision laser cut, TIG welded chassis provides superior support for all the chiller components.
All Flagship Marine air conditioning condensers are hand-crafted from start to finish at our Stuart factory location to our exacting specifications.
Flagship Marine's Sea Water Manifolds
Flagship Marine’s sea water manifolds are 90/10 CuNi schedule 80 pipe, which is MUCH more durable (about 10x thicker!) than our competitors’ tubing. These, in combination with the socolets, meet mil spec requirements and will FAR outlast all others. No sinking or water damage hazard from ruptured hoses or paper thin manifolds at 3AM!
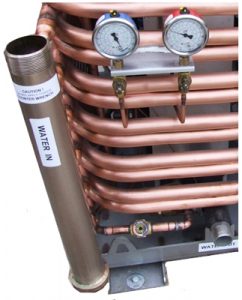
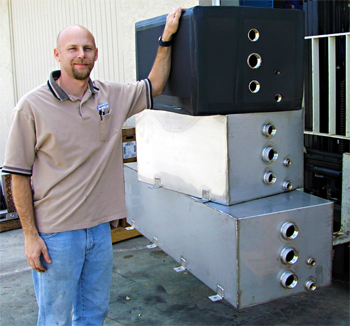
Marine Chilled Water Holding/Storage Tanks
We manufacture a variety of different sized chilled water holding/storage tanks. Shown are 40 and 80 gallon tanks in 14 gauge stainless steel.
Must be on the low pressure return line, and be sure the pump sucks from the bottom of the tank so eliminating air bubbles is easy. You DON’T want the pump to suck a bubble and cavitate!
A small expansion tank open to atmospheric pressure should be placed at a high point.
The holding tank can be at any opportune location, typically in the bilge or engine room immediately before the pump, and is flooded – the expansion tank is plumbed to the top of the holding tank.
Flagship Marine Water Cooled Marine Chillers NEVER Have Condenser Failures!
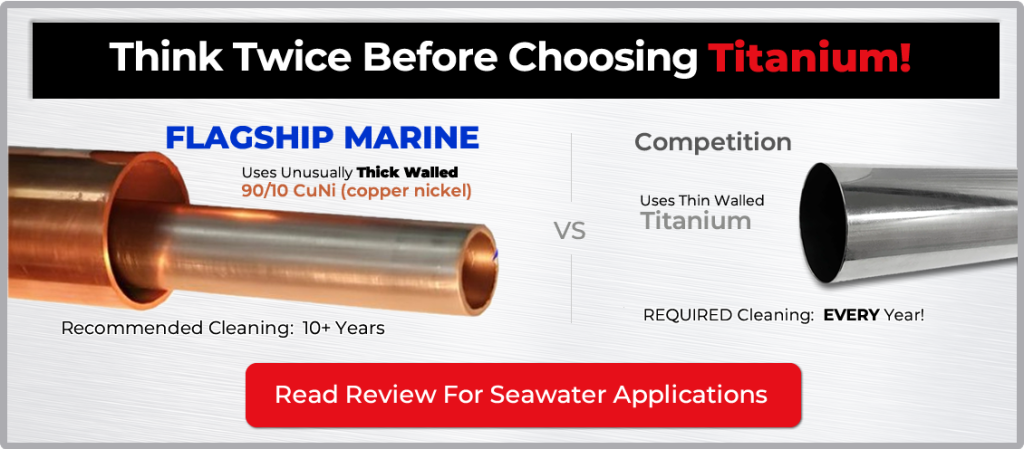
Titanium condensers can be appropriate in some marine applications such as in a power plant where the sea water velocity is greater than 7 feet/second CONSTANTLY – 100% OF THE TIME. This velocity is too fast for barnacle larvae to bond to the metal, and once they do it’s too late!
Titanium has zero anti-microbial properties and when the water is dormant marine growth will take hold very quickly. This is why our competitors state condenser cleaning is REQUIRED at least ONCE/YEAR.
Flagship Marine condensers MIGHT need an acid wash every ten years!
The other big problem with Titanium is brazing it to the condenser shell. One of our major competitors is using steel shells that start to rust in a couple of months, the other major competitor uses a copper shell that fails and offers mechanical seals to repair them.
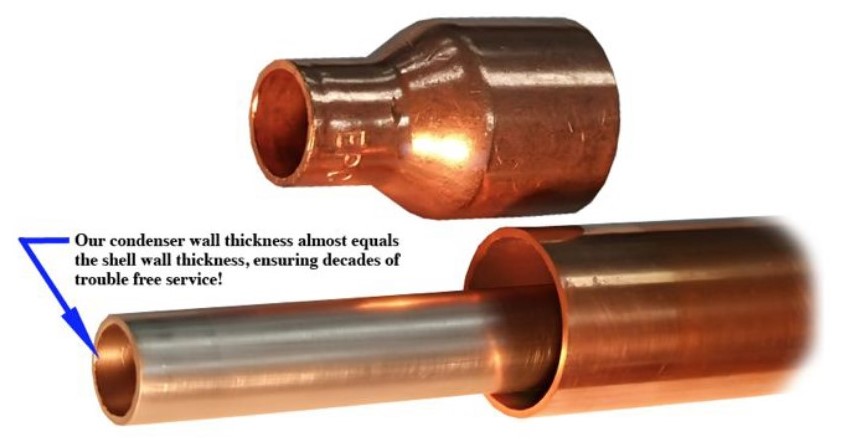
The heart of every marine air conditioner is the condenser – the heat sink to the ocean and the only component the corrosive sea water touches is the inside of the inside tube. Failure of this tube is catastrophic for the entire system.
Even extremely corrosive places like the very high salinity of the Red Sea are no problem for Flagship Marine condensers because we use an unusually thick walled 90/10 CuNi (copper nickel) tube with particular annealment, hardness and other characteristics.
We don’t dramatically shorten our condensers to save money by enhancing this tube: knurling or rifling for example. Our tube is “slick walled” with no thin spots for marine growth to find a foothold. Paper thin condenser tubes dissipate heat very quickly so the condenser tube can be short and inexpensive. We don’t cut corners by doing so. We have full length condensers!
The shorter the condenser, the cheaper it is and the shorter it will last!
As a result, Flagship Marine is very proud to have had almost
ZERO condenser failures in the last two decades.
MARINE AIR CONDITIONING CHILLER SAFETY FEATURES
Dual Safety Switches In Parallel
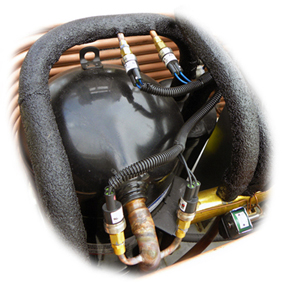
10,15,and 30 ton GEA Evaporators
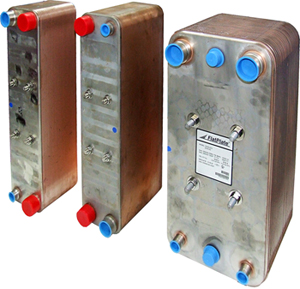
Hi-Max PVC manifolds
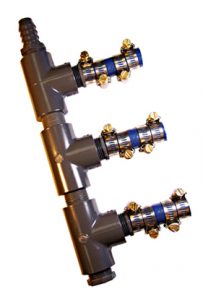
Superior Modulation Of The A/C Refrigerant
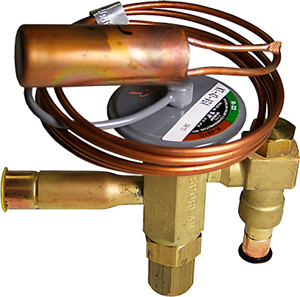
EXPANSION VALVES VS. CAPILLARY TUBES
All Flagship Marine air conditioners incorporates expansion valves which adjust the modulation of the refrigerant to match the conditions of sea water, humidity and ambient temperature. This maximizes performance by preventing excessive or inadequate refrigerant head pressures, resulting in more cooling and extended component life!
This is why all new HVAC equipment must now use expansion valves instead of the capillary tubes you may still have in your home air conditioner. We don’t “cut corners” – these cost us about $75-175 each vs a $3.00 cap tube, and on the larger units we use “balanced port” rather than the standard expansion valves which automatically adjust to the amount of refrigerant flowing rather than being a fixed flow and out of balance.
Single Evaporator Chilled Water Fan Coil Features
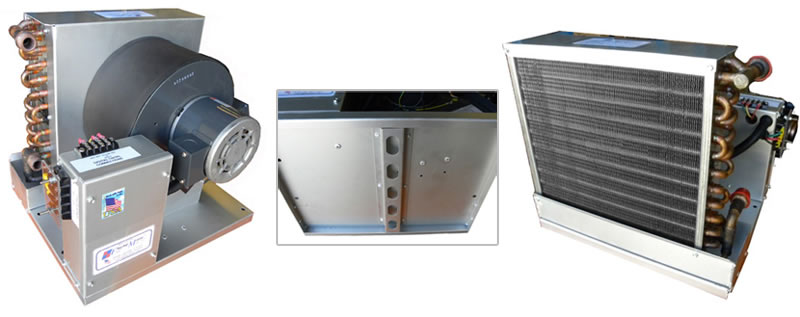
- Precision-engineered 16-gauge anodized aluminum chassis, drain pan and evaporator housing are lightweight and corrosion resistant.
- Drain pan under the evaporator only. This results in a dry chassis and no condensate sloshing.
- Engineered hat-section reinforcing plat provides exceptional strength and lightweight
- Incredibly rugged and simple over-the-counter components in and electric box – no proprietary, expensive printed circuit boards.
- Whisper-quiet Dayton split-pole blower motors, absent the humming sounds of variable speed DC motors.
Optional Heat
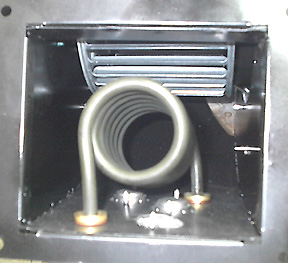
The optional heat can be one of our legendary incoloy clad electric elements in the fan coil (shown), an in line oil fired boiler, an electric element in the chiller, or reverse cycle.
We prefer the electric elements in the fan coils because the entire system is shut down when in the heating season – the only moving part is the blower motor when heat is called for. We have had tens of thousands of these elements in service for many years – they are extremely safe and basically indestructible.
Considering a Mini Split System?
This fairly new innovation has one variable speed condensing unit supplying refrigerant to up to eight small remote evaporators. This can result in a very significant savings to the end user in certain situations, such as a home, by cooling only the rooms that are occupied.
In a marine application it’s not typical for air conditioned areas to not be occupied, so these savings are not realized in the marine industry. However, the many detriments of these systems remain and they can be acute in a marine application. It’s no wonder why no marine air conditioning manufacturer makes mini split systems. If you do decide to install a residential system on your vessel, you should expect to be replacing the outdoor components quite frequently! Due to the adverse marine environment you might get a couple years out of the condensing unit!
In operation when one of the remote evaporators calls for cooling, the slave board in the remote evaporator sends a signal to the mother board in the condensing unit. This triggers the compressor to ramp up and open the solenoid going to that evaporator to provide refrigerant thus cooling the room.
Every remote evaporator requires its own refrigerant lines connecting it to the condenser. On a typical vessel you will have hundreds of feet of refrigerant lines, half of which are cold return lines that must be insulated. Each evaporator requires separate piping and wiring of the power cable, the refrigerant tubing, the suction tubing, and a condensate drain between itself and the condensing unit. Now imagine all of this buried behind panels, deck heads and cabinetry. This is reminiscent of the split systems of the past which have fallen out of favor in the marine industry over the years because of the ongoing maintenance and down time due to relentless refrigerant leaks caused by rotted copper lines and leaking brazed joints that are so hard to locate.
Imagine the difficulty a technician will have trying to sniff out a leak that could be anywhere along these hundreds of feet of refrigerant lines. At least every 50′ (the length of a roll of copper tubing) you have a brazed joint, and these lines are buried in the structure of the moving/flexing vessel. With a SINGLE leak the ENTIRE system is down!
As proven time and time again there is “no free lunch” with thermodynamics, so the tonnage is the same resulting in no weight or current savings. The only way to save weight is to use thin sheet metal and other inferior components. If the load is 12 tons you will need twelve tons of cooling regardless of the type of system – you will NOT be running a mini split system at 25% capacity at high noon with a hundred people on board! It will be 100%! A chiller system works the same way so at 10PM your Flagship Marine chiller might be running ten minutes/hour, so the total current consumption will be basically the same with any system.
The condensate is oftentimes problematic because it can be difficult finding a sensible means of running a condensate drain from every remote wet evaporator. Sometimes it’s easier to run dry ducting rather than install wet evaporators.
In conclusion, we believe a chiller system in these applications is much more desirable, and especially with Flagship Marine equipment you will have ZERO expensive/proprietary printed boards that can cost you a small fortune over the years. Mini splits are the MOST complicated/complex systems electronically. Printed circuit boards and naked copper tubing don’t do well on a moving, flexing vessel in a marine environment!
Reduced Voltage Fluctuation
Variable Frequency Drives And Digital Scroll Compressors?
If your vessel is wired single phase or you have marginally sized generators, or if you want to almost completely eliminate voltage fluctuation when compressors start, we can install Variable Frequency Drives (VFDs) in our equipment.
The VFD reduces the start up inrush and will greatly reduce any brown out, generator lag or flickering in your TV when the compressors start.
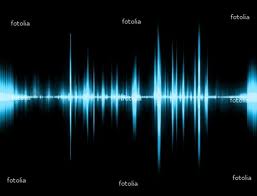